With modern manufacturers coming under growing pressure to cut costs and retain skilled staff in a challenging job market, businesses are searching for new solutions that allow them to maximise efficiency without compromising on quality or safety. End-of-line palletising, powered by innovative collaborative robots, presents a new way for manufacturers to streamline their operations and increase productivity while enhancing workplace safety.
Introducing collaborative robots
Collaborative robots (also known as ‘cobots’) can handle demanding palletising tasks with efficiency and ease. These advanced robots combine strength and precision, making them ideally suited for industries that require the unique blend of heavy lifting and delicate handling. With their extended reach and high payload capacity, specialised cobots can effortlessly lift and stack heavy boxes, while their precise movements ensure that each pallet is built with consistent quality, reducing the chance of errors and minimising and potential damage to products.
In addition to their physical capabilities, with the right integration partner, cobots can connect seamlessly with modern palletising software. This allows manufacturers to easily manage multiple SKUs, even when dealing with a variety of box sizes and weights. By eliminating the complexity associated with traditional systems, cobots offer manufacturers greater flexibility and control, ensuring that they can quickly adapt to changing demands with minimal effort and downtime.
Of course, a key requirement for any robotic system operating in a shared workspace is safety. This is why modern palletising systems are equipped with state-of-the-art scanners that continuously monitor the workspace, creating a virtual safety zone around the robot. If a worker or object breaches this zone, the system reacts instantly, either slowing down or stopping the robot’s operation entirely depending on how it’s configured. This approach helps prevent accidents and enables robots and humans to work in a shared, collaborative space with minimal risk.
In addition to safeguarding workers, these safety features enable companies to comply with strict workplace regulations, reducing potential liabilities. The safety scanners also eliminate the need for extensive physical barriers, freeing up valuable floor space and supporting the creation of more flexible layouts.
The benefits of robotic palletisers
- Improved efficiency and productivity
Automated palletising drastically reduces the time and labour required to complete repetitive tasks. By offloading these tasks to a robot, workers can spend less time on manual labour and instead focus on more complex, value-adding activities that benefit from human input.
- Consistency and accuracy
Every human worker has their own approach to palletising, which means that the quality and layout of a pallet can vary. In contrast, a cobot offers repeatability and precision with every cycle. This consistency ensures that each pallet is stacked uniformly, reducing the risk of product damage during transportation.
- Flexibility for multiple SKUs
When deployed with the right systems integrator, a cobot can handle a wide range of SKUs, allowing businesses to build pallet configurations and deploy them when running that product. This flexibility allows manufacturers to quickly adapt to changing production needs without significant downtime, making a collaborative robot system an ideal choice for businesses with diverse product lines.
- Reduced labour costs and ergonomic strain
Manual palletising can be physically demanding, leading to potential injury and fatigue among workers. By automating this task, businesses not only reduce the risk of worker injury but also save on labour costs associated with manual handling. The cobot handles the heavy lifting, while human workers stay focused on more critical tasks.
The importance of integration
While robotic palletisers can bring several advantages to production lines, the key to realising their full potential lies in the seamless integration with existing systems. Robots, no matter how advanced, cannot operate in a vacuum and must communicate effectively with software and hardware across the factory floor. This is where a trusted system integrator becomes essential.
Optimal Industrial Automation, for example, specialises in providing the tools and expertise needed to integrate robotic systems into existing setups. Whether it’s ensuring smooth data exchange between the robot and a business’ computer systems or configuring software for real-time performance monitoring, Optimal’s role as an integrator is to bridge the gap between innovative technology and practical application.
A smarter, safer choice
Robotic palletisers represent a smarter, more efficient future for manufacturers, and with the right system integration, businesses can realise the full extent of their capabilities. By partnering with experts like Optimal Industrial Automation, manufacturers can streamline their operations, increase productivity, and create a safer, more cost-effective work environment.
To learn more about how Optimal can help you integrate robotised palletising solutions into your production line, visit our website or contact our team today.
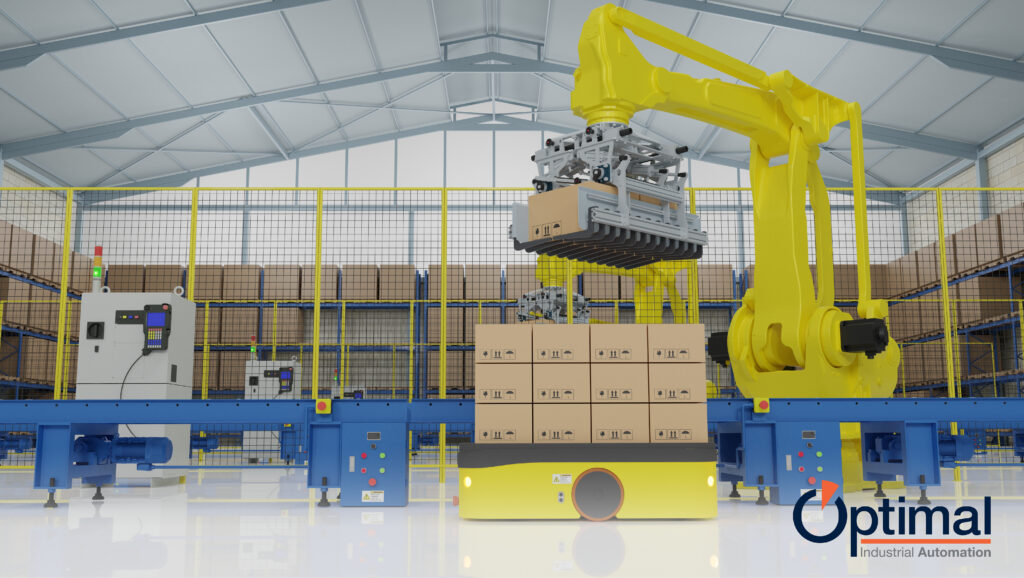
Image 1: While robotic palletisers can bring several advantages to production lines, the key to realising their full potential lies in the seamless integration with existing systems.