Jun 20, 2023
The need for more sustainable practices in the food and beverage industry is gaining pace, driven by new regulations, market demands as well as the desire to combat climate change and save costs. When looking at cutting emissions and reducing energy consumption, there are a number of automation-driven solutions that can deliver noticeable gains quickly and efficiently. These enable companies to stay ahead of the competition and meet global 2030 and 2050 targets.
Martin Gadsby, VP at Optimal Industrial Automation & Optimal Industrial Technologies, looks at key automation applications that can be implemented quickly to support expedited decarbonization strategies.
To successfully shrink their environmental footprint, food processors should begin by favoring solutions that can address their most pressing issues whilst setting the backbone for future improvements. These are key to supporting healthy business growth, delivering a quick return on investment (ROI) as well as enabling companies to continuously improve their efficiency and environmental performance.
Obtaining working information fed back from an operational plant will help an engineering manager choose the best project to implement going forward, in terms of ROI and environmental impact. In practice, the most suitable strategies revolve around the use of data. The data can be analyzed in real time and the results fed back to the plant control systems so that they can optimize the process, within allowed limits, to reduce the waste of both raw materials and final product.
The role of energy meters
A value-adding first step for food processors in their sustainability journey is the installation of accurate energy monitoring systems. To succeed in a step-by-step implementation, companies can begin by tracking usage of the most power-intensive equipment and then expanding the coverage to more assets, until the entire plant is supervised.
This strategy helps processors gain real-time, actionable insights that can assist in identifying inefficiencies and rectifying them to conserve energy. As more data is acquired, it is also possible to gather energy trends over the course of the day, empowering companies to schedule power use, e.g. reducing it when the cost per unit is expected to spike.
Adopting a holistic approach to process management
Another similar data-driven control solution is the adoption of Process Analytical Technology (PAT), which can be used to monitor individual assets all the way to entire plants, following a stepwise approach. This framework provides real-time intelligence on product quality and the processes involved, enabling companies to promptly change operating conditions to maximize the end results.
Through PAT, it is therefore possible to reduce off-spec and associated waste and reworks, optimizing resource and energy usage and ultimately improve the environmental performance of food processing activities. In addition, the accurate overview provided can help avoid operational inefficiencies that lead to excessive energy use, such as overprocessing as well as unnecessarily high temperatures.
Furthermore, as PAT offers a comprehensive overview of the critical quality attributes (CQAs) of products as they go through different lines and treatments, it empowers companies to increase the flexibility in their feedstock. More precisely, they can adopt greater local resources that may have varying specifications, for example selecting native sucrose-rich crops for sugar production.
Similarly, food companies can begin to use a wider range of raw materials, including those obtained from in-house processes or from suppliers (as, for example, by-products), to optimize the value that can be extracted from them.
Following an initial characterization of their properties and in line with real-time results from PAT analytical investigations, operating conditions can be adjusted to maintain the quality of the final product, across a range of raw material characteristics. Moreover, the knowledge generated by PAT can help companies identify valuable elements within their waste and by-products that can be sold and repurposed, supporting circularity in the industry while generating additional revenue streams.
Ultimately, thanks to the power of data, food processors can combine their sustainability and digitalization journeys to drive efficiency, productivity and competitiveness. The Optimal Group, formed by Optimal Industrial Automation and Optimal Industrial Technologies, has been supporting multiple food processors as well as businesses in a variety of sectors to improve their environmental footprint and readiness to Industry 4.0 by means of bespoke state-of-the-art, data-driven control systems.
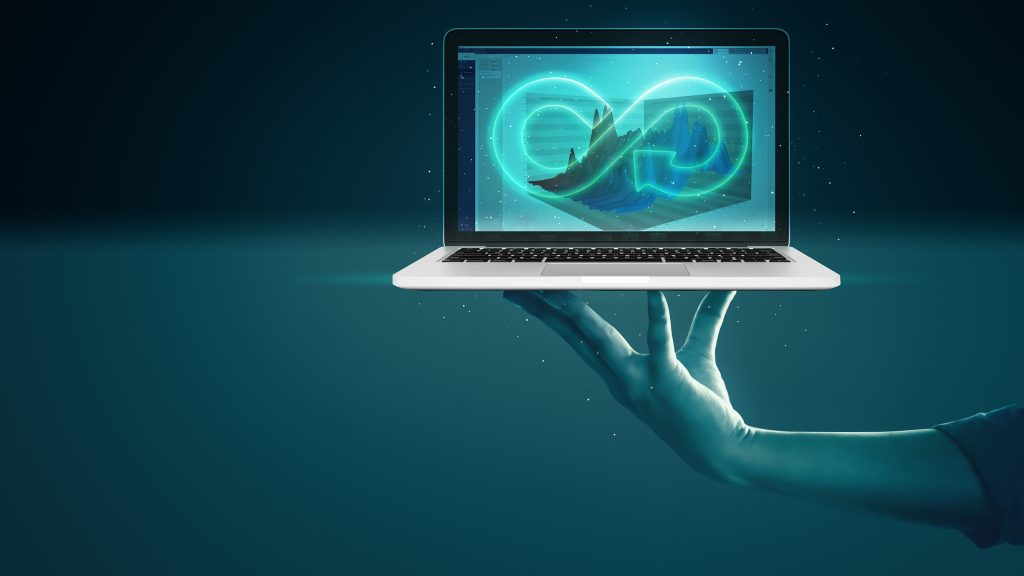
Image 1: Thanks to the power of data, food processors can combine their sustainability and digitalization journeys to drive efficiency, productivity and competitiveness.
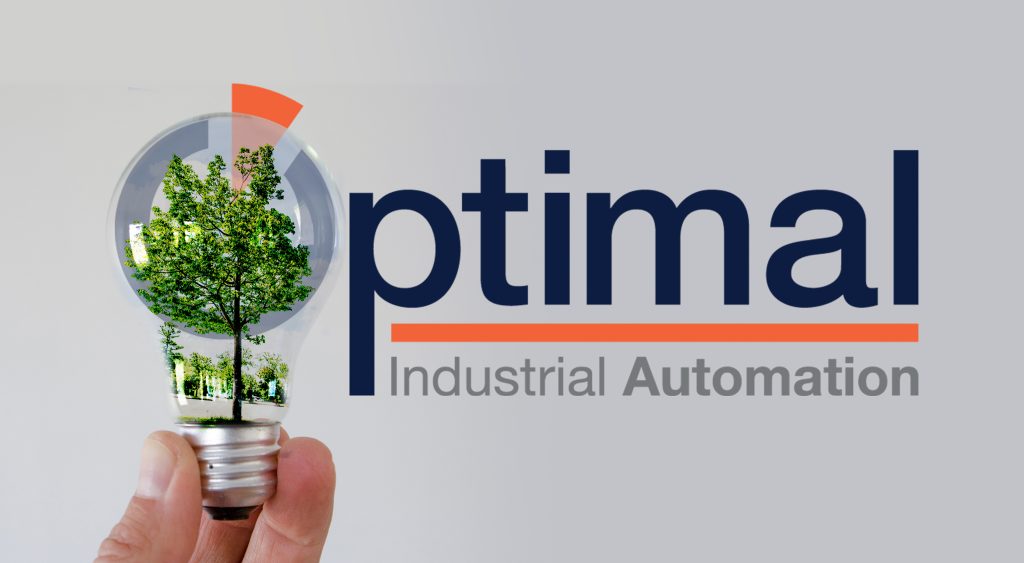
Image 2: The Optimal Group has been supporting multiple food processors as well as businesses in a variety of sectors to improve their environmental footprint and readiness to Industry 4.0.